Т.В. Алесинская
Основы логистики. Функциональные области логистического управления
Таганрог: Изд-во ТТИ ЮФУ, 2009. 79 с.
2. ЛОГИСТИКА ЗАПАСОВ
2.3. Модели управления запасами
Управление запасами заключается в решении двух основных
задач:
1) определение
размера необходимого запаса, т.е. нормы запаса, и частоты его пополнения;
2)
создание системы контроля за фактическим размером запаса и своевременным
его пополнением в соответствии с установленной нормой.
Норма запаса – расчетный минимальной уровень
запасов, который должен быть на складе предприятия для обеспечения
бесперебойного снабжения производства продукции или реализации товаров. Для
определения норм запасов используют три группы методов: эвристические методы, методы
технико-экономических расчетов и экономико-математические методы.
Эвристические методы предполагают
использование опыта специалистов, которые изучают отчетность за предыдущий
период, анализируют рынок и принимают решения о минимально необходимых запасах,
основанные, в значительной степени, на субъективном понимании тенденций
развития спроса. В качестве специалиста может выступать работник предприятия,
постоянно решающий задачу нормирования запасов. В этом случае метод решения
задачи называется опытно-статистическим. Если используется опыт сразу
нескольких специалистов, то их субъективные оценки ситуации анализируются по
специальному алгоритму, проверяются на непротиворечивость и трансформируются в
окончательное решение, близкое к оптимальному. Такой метод называется методом экспертных
оценок.
Метод технико-экономических расчетов заключается
в разделении совокупного запаса в зависимости от целевого назначения на отдельные
группы, например, номенклатурные или ассортиментные позиции. Затем для этих
групп отдельно рассчитываются страховой, текущий и сезонный запасы. Каждый из
этих уровней также может быть разделен на более мелкие составляющие, например,
страховой запас на случай нарушения поставок, или страховой запас на случай
увеличения спроса и т.д. Метод технико-экономических расчетов позволяет
довольно точно определять необходимый размер запасов, но отличается большой
трудоемкостью. Такой подход используется также в системе MRP
(см. п.7.5.2 [2]).
Экономико-математические методы позволяют определять
норму запаса на основе построенных математических моделей УЗ, либо с помощью методов
экстраполяции прогнозировать будущий запас на основе темпов изменения и
тенденций в образовании и запасов в предыдущем периоде.
Эффективность работы систем УЗ во многом зависит от того,
насколько точно будет предсказан спрос на ресурс и, следовательно, насколько
правильно будет проведено нормирование. Это является довольно сложной задачей.
Выделяют следующие типы спроса по степени определенности и неизменности его
величины (рис.2.3)
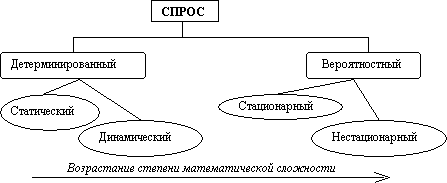
Рис.2.3.
Классификация типов спроса
Детерминированный спрос точно известен
заранее, в отличие от вероятностного спроса. При статическом типе
спроса интенсивность потребления ресурса остается неизменной во времени, при динамическом
типе спроса интенсивность потребления изменяется в зависимости от времени. При стационарном
типе спроса его функция плотности вероятности неизменна во времени, а при нестационарном – функция плотности вероятности спроса изменяется
во времени.
По признаку источника возникновения спрос разделяют на
независимый и зависимый. Независимый спрос – спрос, который
складывается из отдельных составляющих спроса большого числа потребителей,
каждый из которых испытывает потребность независимо от других. Зависимый
спрос имеет место, когда производитель использует ряд компонентов для
изготовления ГП, спрос на каждый из компонентов связан друг с другом и зависит
от производственного плана изготовления ГП.
При независимом типе спроса используется подход, при котором
запасы не связываются с производственными планами, и поэтому они должны быть
достаточно высокими, чтобы удовлетворить любой возможный спрос. Эти запасы
снижаются во время производства, но вскоре снова пополняются. Общая динамика
изменения запасов при независимом и зависимом спросе показана соответственно на
рис. 2.4 (a) и (б).
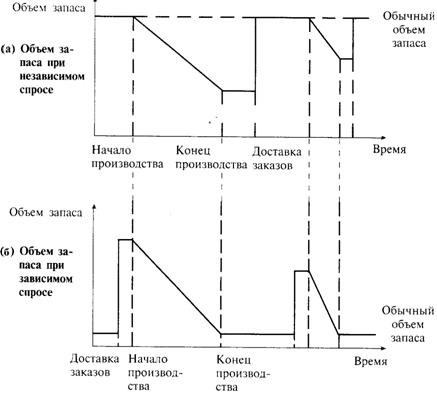
Рис.2.4. Сопоставление динамики изменения
объема запасов
при зависимом и
независимом спросе
При наличии зависимого спроса может быть использован подход MRP –планирования потребности в материалах (material requirements planning) (см. п.7.5.2 [2]). Суть
этого подхода заключается в расчете потребностей во всех видах материалов,
сырья, комплектующих, деталей, необходимых для производства каждого продукта из
плана производства в требуемом объеме, и подаче соответствующих заказов на
поставку. В расчетах используются ведомости спецификации – упорядоченный список всех составляющих, необходимых
для производства конкретного продукта.
Еще одним способом планирования является подход "точно
в срок" (just in time) или JIT (см. п.7.5.4 [2]). Цель JIT – обеспечение доставки материалов непосредственно ко
времени выполнения конкретных операций, благодаря чему запас фактически
уничтожается. На рис. 2.5 представлены объемы запасов при различных
подходах к планированию.
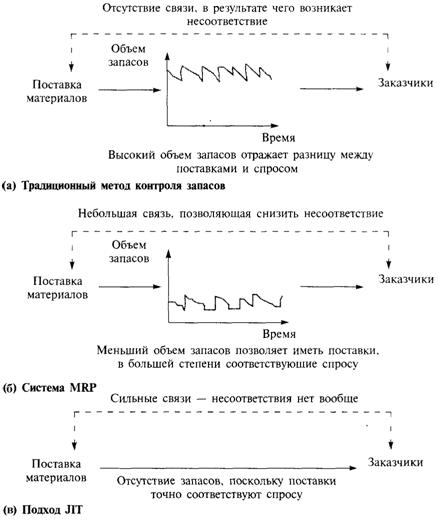
Рис. 2.5.
Уровень запасов при различных подходах к управлению запасами
Причиной снижения уровня запасов, показанной на
рис. 2.5 (б) и (в), является увеличивающая координация между спросом на
рынке сбыта и спросом предприятия на материалы, поставляемые поставщиками.
Обобщенная модель оптимальной партии поставки с учетом невыполненных заявок
Входные параметры модели
1)
n – интенсивность
потребления запаса [ед.тов./ед.t];
2)
l – интенсивность
производства заказа [ед.тов./ед.t];
3)
s – затраты на хранение запаса [руб./ед.тов.*ед.t];
4)
d – штраф за дефицит [руб./ед.тов.*ед.t];
5)
K – затраты на осуществление заказа [руб.].
Выходные параметры модели
1)
Q – размер заказа [ед.тов.];
2)
t – период поставки [ед.t];
3)
–длительность
i-го этапа цикла изменения запаса;
4)
L – общие затраты на управление запасами в единицу времени,
[руб./ед.t];
5)
Н – максимальный уровень запаса на складе [ед.тов.];
6) h – максимальный уровень дефицита [ед.тов.].
Данная модель основана на допущении, что существует
производственный процесс, в котором на первом станке производится партия деталей
с интенсивностью , которые используются на втором
станке с интенсивностью (рис.2.6).

Рис.2.6.
Принципиальная схема производственного процесса
Невыполненные заявки на потребляемый продукт накапливаются и
немедленно удовлетворяются по мере новых поступлений продукта. Длительность
цикла изменения запасов разделяется на 4 этапа (рис.2.7):
1)
t1 – заказанный
продукт производится, произведенный продукт потребляется ® запас накапливается;
2)
t2 – заказанный
продукт не производится, запас потребляется ®
запас уменьшается до нуля;
3)
t3 – заказанный
продукт не производится, запас отсутствует ®
невыполненные заявки накапливаются, дефицит увеличивается;
4) t4 – заказанный продукт производится,
задолженные заявки выполняются ®
запас отсутствует, дефицит уменьшается до нуля.
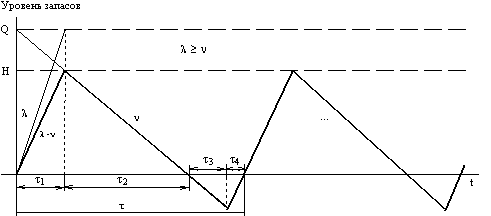
Рис.2.7.График
циклов изменения запасов в обобщенной модели УЗ
с учетом невыполненных
заявок
Формулы модели
; ; ;
; ; ; ;
; .
Обобщенная модель оптимальной партии поставки с потерей невыполненных
заявок
Данная модель характеризуется
тем, что в течение периода t3
заказанный продукт не производится, запас отсутствует, дефицит увеличивается,
но при этом невыполненные заявки не накапливаются, а теряются (рис.2.8). При
этом штраф за дефицит в модели с потерей невыполненных заявок выше, чем в модели
с учетом невыполненных заявок.
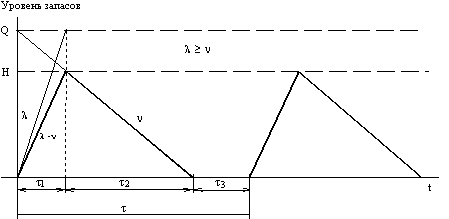
Рис.2.8.График
циклов изменения запасов в обобщенной модели УЗ
с
потерей невыполненных заявок
Формулы модели
; ;
; ; ; ; .
Каждая из рассмотренных обобщенных моделей УЗ имеет по
четыре возможных ситуации УЗ:
1) продукт
производится ( ), дефицит допускается ( ) (см. рис.2.7,
2.8);
2) продукт
закупается ( ), дефицит допускается ( );
3) продукт
производится ( ), дефицит запрещен ( );
4) продукт
закупается ( ), дефицит запрещен ( ) – модель
Уилсона (рис.2.9).
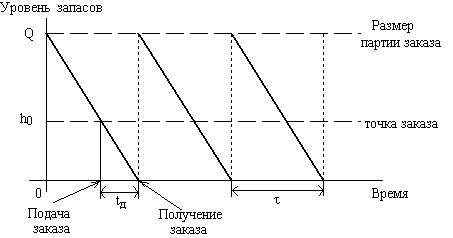
Рис.2.9.
График циклов изменения запасов в модели Уилсона
Модель УЗ, учитывающая скидки
Данная модель учитывает возможность предоставления скидок
покупателю при покупке партии товара определенного размера. При этом заказы на
более крупные партии с одной стороны повлекут за собой снижение затрат на
закупку и доставку, а с другой стороны – увеличение затрат на хранение.
Таким образом, оптимальный размер заказа может изменяться по сравнению с ситуацией
отсутствия скидок. Подробное описание модели УЗ, учитывающей скидки, приведено
в п.12 [3].
В реальных условиях УЗ некоторые параметры могут меняться в
течение определенного планового периода по следующим причинам:
·
изменение
интенсивности потребления в ту или другую сторону;
·
задержка или
ускорение поставки;
· поставка незапланированного объема
заказа;
· ошибки учета фактического запаса,
ведущие к неправильному определению
размера заказа.
В табл.2.1 представлены возможные возмущающие воздействия, приводящие
систему в состояние либо дефицита
МЗ, либо складских площадей. На практике могут
иметь место разнообразные сочетания
воздействий, перечисленных в правом и левом столбцах табл.2.1.
Таблица 2.1
Возможные возмущения в системе управления запасами
№
|
Дефицит МЗ
|
Дефицит складских площадей
|
1
|
Увеличение
потребления
|
Сокращение
потребления
|
2
|
Задержка поставки
|
Ускоренная поставка
|
3
|
Неполная поставка
|
Поставка
завышенного объема
|
4
|
Занижение размера
заказа
|
Завышение размера
заказа
|
В описанных ситуациях статические модели УЗ не работают,
и поэтому необходимо применять динамические модели УЗ, в которых
предусмотрен механизм адаптации к изменяющейся ситуации.
Другой особенностью статических моделей УЗ, которая
неприемлема в описанных условиях, является использование
критерия минимизации совокупных затрат на хранение запасов и доставку заказов. Такой критерий не имеет смысла в
ситуациях, если
· время исполнения заказа довольно продолжительно;
· поставки часто происходят с
задержками;
· спрос испытывает существенные колебания;
·
цены на заказываемые сырье, материалы,
полуфабрикаты и прочее сильно колеблются.
В таком случае нецелесообразно экономить на содержании
запасов. Это может привести к невозможности
непрерывного обслуживания потребителя, что не соответствует цели функционирования логистической системы УЗ. Во всех других ситуациях определение оптимального размера заказа
обеспечивает уменьшение издержек на хранение запасов без потери качества
обслуживания.
К основным динамическим системам УЗ относят:
1)
систему с фиксированным размером заказа;
2)
систему с фиксированным интервалом времени
между заказами.
Система УЗ с фиксированным размером заказа
Основная
идея модели. Размер
заказа в этой системе – основополагающий параметр, который определяется в первую очередь. Он строго зафиксирован и не
меняется ни при каких условиях работы
системы. Заказ подается в момент, когда текущий запас достигает порогового
уровня. Если поступивший заказ не пополняет систему до порогового уровня, то
новый заказ производится в день поступления заказа.
|
Движение запасов в системе с
фиксированным размером заказа графически представлено на рис.2.10.
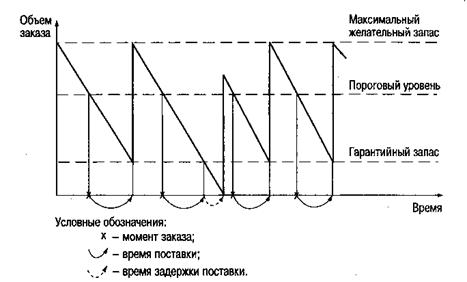
Рис.2.10. Графическая модель работы системы УЗ
с фиксированным размером заказа
Пороговый уровень запаса
рассчитывается как объем запаса, который будет потреблен за время доставки с
учетом сохранения страхового запаса. При отсутствии сбоев в поставках
поступление заказа происходит в момент, когда размер запаса достигает страхового
уровня. Страховой запас позволяет обеспечивать потребность на
время максимально возможной предполагаемой задержки поставки. Восполнение
страхового запаса производится в ходе последующих поставок. При отсутствии
сбоев в поставках и оптимальном размере поставки запас пополняется до максимального
желательного уровня. В отличие от страхового и порогового максимальный
желательный запас не оказывает непосредственного воздействия на
функционирование системы в целом. Этот уровень запаса определяется для
отслеживания загрузки площадей.
Порядок расчета параметров системы
управления запасами с фиксированным размером заказа в общем случае представлен
в табл.2.2.
Таблица 2.2
Параметры системы УЗ с
фиксированным размером заказа
№
|
Входные
параметры
|
Обозначение
|
1
|
Интенсивность
потребления, , шт./ед.t
(при расчете
округление в большую сторону)
|

|
2
|
Время доставки
заказа, ,
ед.t
|

|
3
|
Максимально возможная
задержка в поставках, , ед.t
|

|
4
|
Стоимость доставки, K,
руб.
|
K
|
5
|
Стоимость хранения запаса, s,
руб./(шт.*дн)
|
s
|
|
Выходные
параметры
|
Расчет
|
6
|
Оптимальный
размер заказа, , шт.
|

|
7
|
Страховой запас,
, шт.
|

|
8
|
Пороговый
уровень запаса, , шт.
|

|
9
|
Максимальный
желательный запас, , шт.
|

|
Необходимость
постоянного учета
запаса в системе с
фиксированным размером заказа можно рассматривать как основной ее недостаток. Кроме того, эта система не ориентирована на учет неоднократных сбоев
в объеме поставок. Они могут приводить ее в дефицитное состояние, которое
может усугубляться задержкой следующих поставок (рис.2.11). Для
исправления подобной ситуации необходимо потребовать от поставщика одноразового
увеличения объема поставки, что позволит пополнить
запас до максимального желательного уровня.
Система управления запасами с фиксированным интервалом времени между
заказами
Основная
идея модели. В системе с фиксированным интервалом времени между
заказами заказы делаются в строго определенные моменты времени через равные
интервалы времени (например, два раза в неделю или 1 раз в месяц и т.п.).
Поскольку момент заказа заранее определен и неизменен, то постоянно
пересчитываемым параметром является объем заказа. Объем заказа определяется по принципу
восполнения запаса до максимального
желательного уровня с учетом потребления за время поставки.
|
Графическая модель работы системы УЗ с фиксированным интервалом
времени между заказами представлена на рис.2.12.
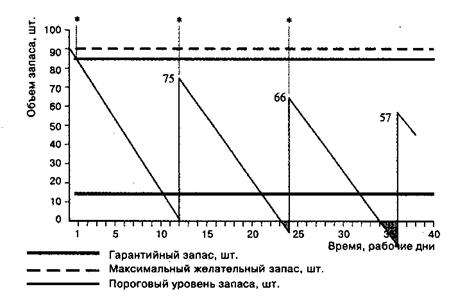
Рис.2.11. Графическая модель работы
системы УЗ с фиксированным размером заказа при наличии неоднократных задержек в
поставках
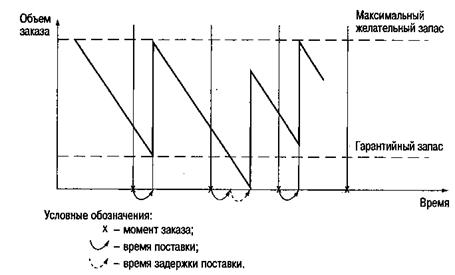
Рис.2.12. Графическая
модель работы системы УЗ
с фиксированным интервалом времени
между заказами
Порядок расчета параметров системы управления запасами
фиксированным интервалом времени между заказами представлен в табл.2.3. Интервал
времени между заказами (период поставки) обычно рассчитывают, а
затем могут корректировать. Например, при
полученном расчетном результате 4 дня можно использовать период 5 дней, чтобы подавать заказы один раз в неделю.
Описанные выше основные системы УЗ базируются на фиксации
одного из двух возможных параметров – размера заказа или интервала времени
между заказами. Но при наличии систематических сбоев в поставке и
потреблении основные системы УЗ становятся неэффективными.
Таблица 2.3
Параметры системы УЗ с
фиксированным интервалом времени
между заказами
№
|
Входные
параметры
|
Обозначение
|
1
|
Интенсивность
потребления, , шт./ед.t
(при расчете
округление в большую сторону)
|

|
2
|
Время доставки
заказа, ,
ед.t
|

|
3
|
Максимально возможная
задержка в поставках, , ед.t
|

|
4
|
Стоимость доставки, K,
руб.
|
K
|
5
|
Стоимость хранения запаса, s,
руб./(шт.*дн)
|
s
|
|
Выходные
параметры
|
Расчет
|
6
|
Период поставки, , ед.t
|

|
7
|
Страховой запас,
, шт.
|

|
8
|
Максимальный
желательный запас, , шт.
|

|
9
|
Объем заказа, Q,
шт.
|

|
|
где – текущий
запас с учетом заказанного, но не доставленного товара
|
Различные сочетания звеньев основных систем УЗ вместе с
добавлением принципиально новых идей приводит к возможности формирования
большого количества других систем УЗ, отвечающих самым разнообразным
требованиям.
К наиболее распространенным модификациям основных
динамических систем УЗ относят:
1) систему с установленной периодичностью пополнения запасов до
постоянного уровня;
2) систему «минимум—максимум».
Система УЗ с установленной периодичностью пополнения запасов до постоянного
уровня
Основная идея. В данной системе
заказы производятся не только в фиксированные плановые моменты времени, но и при достижении запасом порогового
уровня. Объем заказа определяется
по принципу восполнения запаса до максимального
желательного уровня соответственно от текущего или от порогового
уровня запаса (с учетом потребления за время поставки).
|
Отличительной особенностью системы
является то, что заказы делятся на две категории:
1) плановые Qп, которые подают через заданные интервалы времени t;
2) дополнительные Qд, при снижении запасов на складе до порогового уровня.
Необходимость дополнительных заказов может
появиться при отклонении темпов потребления от запланированных.
Таким образом, данная система включает в себя элемент
системы с фиксированным интервалом времени между заказами (установленную
периодичность оформления заказа) и элемент системы с фиксированным размером
заказа (отслеживание порогового уровня запасов). В отличие от основных систем
она ориентирована на работу при значительных колебаниях потребления.
Графическая иллюстрация функционирования системы УЗ с установленной периодичностью пополнения запасов до
постоянного уровня приведена на рис.2.13. Порядок расчета всех параметров системы УЗ в общем случае
представлен в табл.2.4.
Система УЗ «минимум-максимум»
Основная
идея. В данной системе заказы производятся в фиксированные плановые моменты времени, но при условии, что текущий запас в этот момент равен или меньше установленного минимального (порогового)
уровня. Объем заказа определяется
по принципу восполнения запаса до максимального
желательного уровня (с учетом потребления за время поставки).
|
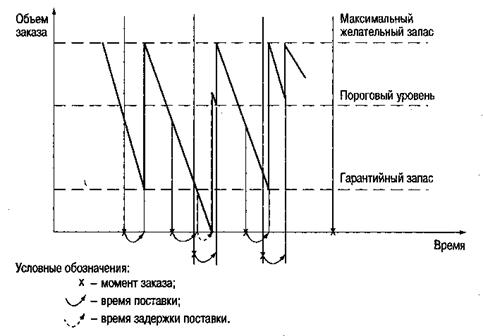
Рис.2.13.
Графическая модель работы системы УЗ с
установленной периодичностью пополнения запасов до постоянного уровня
Пороговый уровень
запаса в системе «минимум—максимум» выполняет роль «минимального»
уровня. Если в установленный момент времени этот уровень пройден, то заказ
оформляется, в противном случае заказ не выдается. Отслеживание порогового
уровня, а также выдача заказа производятся только через заданный интервал
времени t.
Данная система работает с двумя уровнями запасов – минимальным
(пороговым) и максимальным и содержит элементы системы с фиксированным
интервалом времени между заказами (постоянный интервал между поставками) и
системы с фиксированным размером заказа (использование порогового уровня).
Система «минимум-максимум» ориентирована на ситуацию, когда затраты на учет
запасов и издержки на оформление заказа настолько значительны, что становятся соизмеримы
с потерями от дефицита запасов. Графическая иллюстрация функционирования
системы УЗ «минимум—максимум» приведена на рис.2.14. Порядок расчета всех
параметров данной системы УЗ представлен в табл.2.5.
Таблица 2.4
Параметры
системы УЗ с установленной периодичностью пополнения запасов до постоянного
уровня
№
|
Входные
параметры
|
Обозначение
|
1
|
Интенсивность
потребления, , шт./ед.t
(при расчете
округление в большую сторону)
|

|
2
|
Время доставки
заказа, ,
ед.t
|

|
3
|
Максимально возможная
задержка в поставках, , ед.t
|

|
4
|
Стоимость доставки, K,
руб.
|
K
|
5
|
Стоимость хранения запаса, s,
руб./(шт.*дн)
|
s
|
|
Выходные
параметры
|
Расчет
|
6
|
Период поставки, , ед.t
|

|
7
|
Пороговый
уровень запаса, , шт.
|

|
8
|
Страховой запас,
, шт.
|

|
9
|
Максимальный
желательный запас, , шт.
|

|
10
|
Объем заказа, подаваемый в
плановые фиксированные моменты времени, , шт.
|

|
11
|
Объем заказа, подаваемый дополнительно
при достижении запасом порогового уровня, , шт.
|

|
|
где – текущий
запас с учетом заказанного, но не доставленного товара
|
Материал предоставлен сайтом AUP.Ru (Электронная библиотека экономической и деловой литературы)
Похожие материалы:
Модели стационарных и нестационарных временных рядов, их идентификация
Модели сбережения, потребления, инвестиций (Алесинская Т.В. и др.)
Модели сбережения, потребления, инвестиций
Моделирование и анализ
многомерных временных рядов
Зубанов Н.В. Анализ устойчивости относительно поставленной цели как один из подходов к описанию функционирования организации в условиях неопределенности: Моделирование неопределенности
Моделирование процессов управления
|